PHOTO: Jeremy stands next to heater treaters on a Bakken well pad.
By Gus Morgan
As an asset and operating integrity inspection coordinator for ConocoPhillips, Jeremy Grabow works to achieve process safety in the Bakken.
Process safety is achieved by using special precautions, or barriers, to keep the company's facilities and products safely contained, eliminating potential impact to people, property or the environment. An unplanned or uncontrolled release of any material (including non-toxic and non-flammable materials) is considered a process safety incident. Enhancing process safety is a key objective for ConocoPhillips.
In 2020, Jeremy led a proactive inspection campaign in the Bakken that measured wall loss in fire tubes, an initiative that improved operational reliability and safeguarded against 26 potential process safety events.
For his efforts, Jeremy won a 2021 SPIRIT of Performance Award, a recognition given to teams and individuals who exemplify ConocoPhillips’ high standards of performance.
What’s a fire tube?
Fire tubes are the heating element in heater treaters, vessels that separate produced fluids (oil, gas and water). Over time, heat can cause fire tubes to corrode. Through corrosion control and process safety management, ConocoPhillips reduces corrosion and replaces heater treaters before they fail and leak.
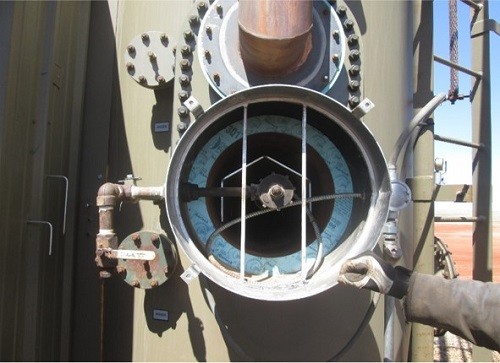
Until recently, the only method to identify corrosion damage in a fire tube was to pull it out and inspect it, a time-consuming and labor-intensive endeavor that would stop production.
“We wanted to find a way to proactively inspect the tubes without stopping production,” he said. “We also wanted to change the design to help extend the life of the fire tubes.”
In addition to design changes, Jeremy suggested a new technology that could revolutionize how Operations managed its fire tubes.
Tech to the rescue
Jeremy contacted a Williston Basin company that specializes in fire-tube inspections to see if they could help.
This company uses a purpose-built scanner for fire-tube inspections. The company’s scanner, a magnetic flux leakage (MFL) tool, can detect corrosion in fire tubes.
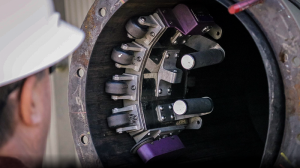
In March 2020, Jeremy convinced Operations to let the contractor inspect five fire tubes in a trial run.
The inspections looked at wall thickness and prioritized fire tubes for proactive replacement based on the severity of the potential hazard.
‘It’s been very effective’
The success of that trial inspection prompted Operations/Facility Engineering to change its practice and process for inspecting and replacing fire tubes to safeguard against potential process safety incidents.
In 2020, hundreds of inspections were performed, and 26 fire tubes were identified for immediate proactive replacement.
Using MFL inspections has also greatly assisted in establishing corrosion rates and remaining service life calculations.
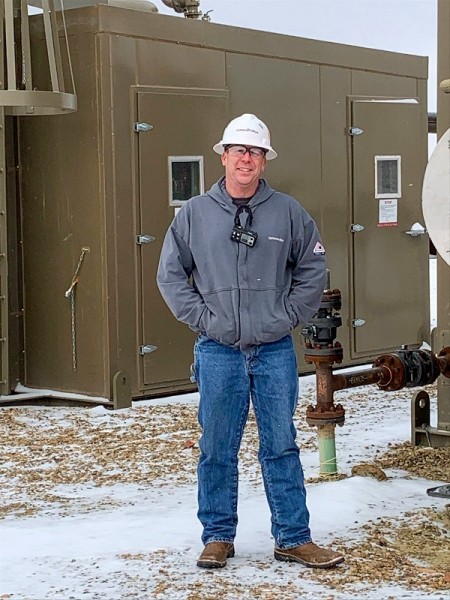
“It’s been very effective,” Jeremy said of the MFL screening tool and process. “It’s fast, efficient and provides great results.”
As part of this process safety initiative, Jeremy created an MFL inspection/accept guide with approval from Facility Engineering. He also worked with Operations and Maintenance to address any corrosion issues.
Moreover, he collaborated with these teams on design changes — such as the installation of heat shields, increasing fire-tube wall thickness and adding sacrificial anodes — to extend the life of the fire tubes.
Jeremy shared his fire-tube learnings with the Permian asset, leading the Delaware team to adopt the MFL inspection method on its fire tubes.
AT A GLANCE
NAME: Jeremy Grabow
JOB TITLE: Senior Asset & Operating Integrity Inspection Coordinator, Lower 48 Great Plains Business Unit
FAST FACTS: Navy veteran; Jeremy worked as a contractor for ConocoPhillips on the North Slope in Alaska for 10 years; he's been a ConocoPhillips employee for nearly seven years
QUICK QUOTE: "ConocoPhillips takes safety to another level."
HOBBIES: Hunting, fishing, vegetable gardening, canning